Activated magnesium oxide can improve the quality of rubber adhesives
Lorem ipsum dolor sit amet, consectetur adipiscing elit. Ut elit tellus, luctus nec ullamcorper mattis, pulvinar dapibus leo.
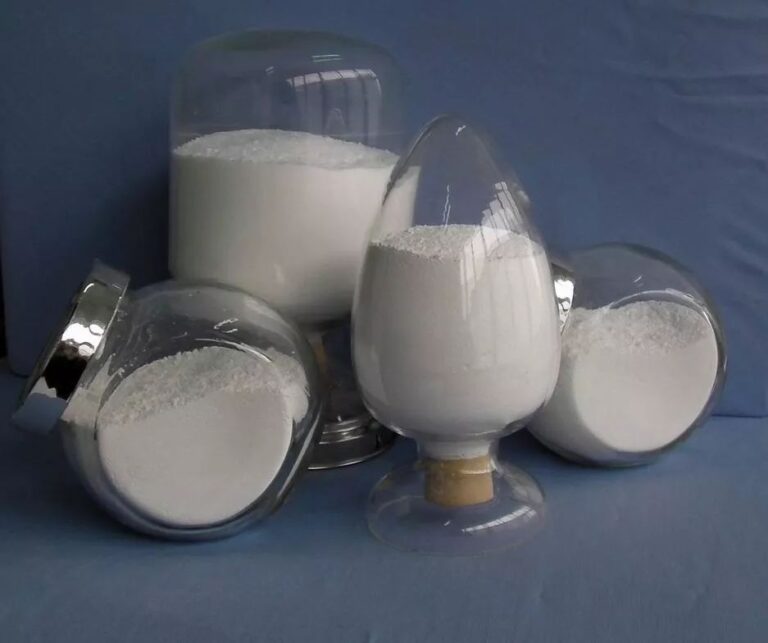
Neoprene adhesive (referred to as neoprene adhesive) is an important variety of rubber adhesive with large output and wide usage. It has high initial adhesion, high bonding strength, flexible adhesive layer, good elasticity, impact resistance, water resistance, oil resistance and alkali resistance. , acid and solvent resistance, ozone resistance, aging resistance, durability and flame retardancy, can bond a variety of metal and non-metal materials.
Ā
Activated magnesia is one of the important raw materials of chloroprene adhesives. Due to its large specific surface area and high activity, activated magnesia is used in chloroprene adhesives to improve the initial adhesion and bonding strength of the adhesive. Improve the transparency of the adhesive. The biggest feature is to prevent the stratification and precipitation of the adhesive. The activity of magnesium oxide reflects the strength of the reaction ability between magnesium oxide and neoprene adhesive. High-quality neoprene adhesives generally use high-activity magnesium oxide. The higher the activity, the faster the reaction with the neoprene adhesive. The role of activated magnesium oxide in chloroprene adhesives is multifaceted, mainly including vulcanization and crosslinking, acid absorption, scorch prevention, and resin chelation.
The main component of neoprene adhesive is not only neoprene rubber, but also resin. Resin has a greater impact on neoprene adhesives. The role of the resin: to improve the adhesion, improve the cohesive strength, and prolong the bond retention time. Commonly used resins: tert-butyl phenolic resin, terpene phenolic resin, petroleum resin, rosin resin, etc. Among them, tert-butyl phenolic resin has the best effect.
If the resin is directly added to the neoprene adhesive, the modification effect is very poor, and it is easy to cause delamination. Only when the resin is pre-reacted with magnesium oxide and then added, can the bonding strength, heat resistance, layer stability and storage stability be significantly improved. Factors such as the quality of the resin, the activity of magnesium oxide, the choice of solvent and catalyst, the reaction temperature, and the reaction time have a great influence on the pre-reaction.