Magnesium oxide (MgO) is a widely used chemical material, with excellent chemical inertness, heat resistance, insulation and thermal conductivity, among which the outstanding high temperature oxidation resistance, moderate alkalinity, due to the presence of oxygen vacancies These properties provide important basic conditions for the application of magnesium oxide.
Generally, magnesia is a flaky crystal, but some special morphologies of magnesia have been found to be very effective in many aspects. For example, spherical magnesium oxide can be used as a stationary phase material in chromatography, can be used as a material for adsorbing toxic substances, and can be added to plastics to improve thermal conductivity. There are very important and effective applications.
The thermal conductivity of high molecular polymer materials is generally low, and the thermal conductivity of most common materials is around 0.3W/m·K.
Therefore, in order to improve the thermal conductivity of high molecular polymer materials, it is necessary to fill thermal conductive fillers in polymer materials. . The thermally conductive filler with high thermal conductivity is uniformly dispersed into the polymer matrix by blending, and a thermally conductive network chain in contact with each other is formed between the fillers, so that the thermal conductivity of the polymer meets the application requirements.
Thermally conductive fillers are mainly divided into three types: carbon-based materials, metal materials and non-metallic inorganic materials. The thermal conductivity of several common fillers is as follows:
1. Carbon-based materials
The thermal conductivity of some carbon-based materials is significantly higher than that of metal materials and inorganic non-metallic materials. Due to the unique microstructure of carbon-based materials, the thermal conductivity of carbon-based materials has anisotropy. Taking graphite as an example, graphite has a typical layered structure, and at the same time plays a role by the dual mechanism of electrons and phonons, so graphite has good thermal conductivity, has anisotropic characteristics, and is cheap and can be well mixed with the matrix , is generally considered to be the preferred thermally conductive filler.
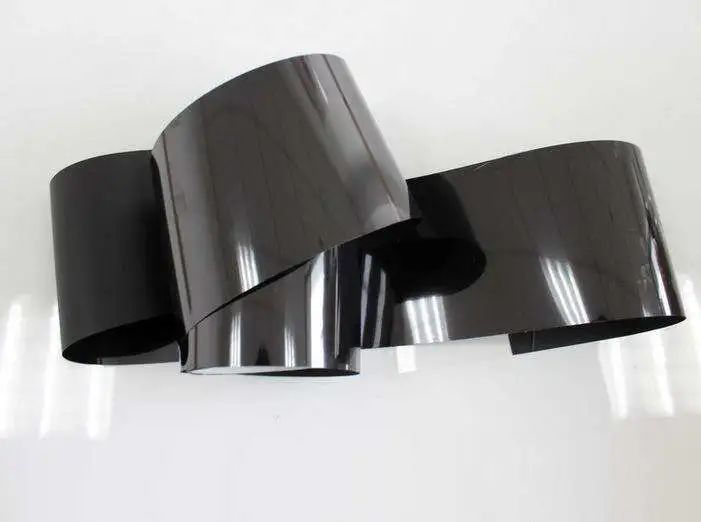
2. Metal material
Metal materials are recognized as good conductors of heat, not only as fillers for polymer materials, but also in aerospace, machinery manufacturing, etc. They are relatively mature and widely used. There are a large number of free electrons inside the metal material, and its thermal conductivity mainly depends on the free movement of the large number of electrons inside. Generally, the thermal conductivity of metal materials is relatively high. At the same time, because the metal material has good electrical conductivity, it can provide electrical conductivity in the composite material prepared as a filler.
However, the density of metal materials is relatively high, and it is difficult to mix uniformly with polymer materials, which restricts its application in thermal conductive fillers of polymer materials.
3. Inorganic non-metallic materials
Inorganic nonmetals mainly rely on phonons to conduct heat. Generally, the thermal conductivity is lower than that of carbon-based materials and metal materials, but they have better insulation. Mainly divided into metal nitrides and metal oxides, metal nitride fillers include: BN, AlN, etc.; metal oxide fillers include: MgO, Al2O3, etc.
Among them, the nitride exists in the form of crystal, the structure is regular and dense, and the propagation resistance of phonons in the crystal is small, so the heat can be transferred more effectively. But the higher the purity of the nitride, the higher the price. Although the thermal conductivity of metal oxides is not high, they are cheap and have a wide range of sources, so they are widely used.
The most commonly used oxides are alumina and magnesia. The thermal conductivity of alumina is relatively low, but the cost is not high, so it is widely used. Although the thermal conductivity of magnesium oxide is lower than that of boron nitride, it is higher than that of aluminum oxide at 36W/m·K, and its cost is lower, so it has attracted more and more attention in the application of thermal conductive fillers.
Effect of different filler morphology on thermal conductivity
Generally, rod-shaped and flake-shaped fillers with a certain length-to-diameter ratio are easier to form a heat-conducting network chain when added to a polymer material, thereby improving the thermal conductivity of the composite material. However, such fillers will have orientation distribution during processing.
That is, the direction of the rod-like structure is inconsistent, which will lead to anisotropy in the thermal conductivity of the composite material, and the thermal conductivity in the processing direction is much higher than that in the vertical processing direction.
Therefore, when designing and producing the shape of the filler product, try to make the orientation of the filler consistent, so as to improve the thermal conductivity of the composite material.
In contrast, due to the isotropy of the spherical structure, the effect of spherical fillers on improving the thermal conductivity of composite materials is more advantageous than that of rod-like or sheet-like structures. At the same time, the particle size of the spherical powder is small and evenly distributed, the surface morphology is regular, and the bulk density of the powder is significantly increased, which can greatly improve the fluidity and dispersibility of the powder, and eliminate the influence of agglomeration to the greatest extent. Improve the defects inside the powder.
Development Status of Spherical Magnesium Oxide
For spherical magnesia products, due to the application of high-performance chip technology, the spheroidization synthesis technology of magnesia is highly confidential abroad, and the international procurement of products is relatively difficult, and it is impossible to obtain complete technical parameters of products and professional manufacturing equipment and other information. According to relevant literature reports, only a few technologically developed countries such as Japan, the United States, and Israel have mastered the synthesis and manufacturing technology of this product in the world.
At present, spherical magnesium oxide is mainly prepared by two methods:
1) The precursor for preparing spherical magnesium oxide is first obtained from magnesium salt, and the precursor is heat-treated to obtain spherical magnesium oxide. Generally, the precursor is spherical basic magnesium carbonate or spherical magnesium hydroxide or spherical basic magnesium oxalate.
2) After the magnesium oxide powder is mixed with solvent and binder, the spherical magnesium oxide is obtained by mechanical molding, and the spherical magnesium oxide product is obtained by heat treatment.
However, in the exploration of industrialization, the spheroidization of magnesium oxide still relies more on the technology accumulation based on spherical alumina and spherical silica powder. In the global scope, Denka is currently at the forefront, and some domestic spherical powder companies are also in the process of Production line layout. It is believed that with the boom in emerging markets such as 5G and new energy vehicles, spherical magnesium oxide, which is regarded as the “next-generation thermal conductive filler” to succeed spherical alumina, can also be mass-produced as soon as possible to achieve localization substitution, thus starting large-scale App promotion.